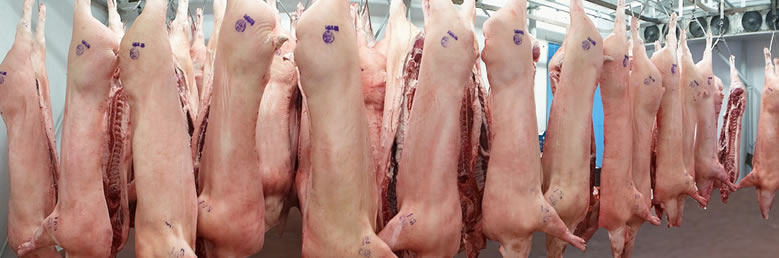
Production:
The productive chain works integrated, from the cultivation of cereals, production of balanced foods, pig production, slaughter, slaughtering and distribution.In addition to this, the incorporation of modern cold stores, providing the plant with an important refrigeration and freezing capacity, which allows an integral management of the cold chain, in the entire production circuit.
Productive structure :
The agroporc farm has 520 pure Landrase females and 50 pure Varkshire stallions, genetically prepared for this purpose.
This genetic alliance results in hybrid pigs with unique characteristics, with ideal breeding skills, which are permanently supervised by personnel specialized in this type of production.
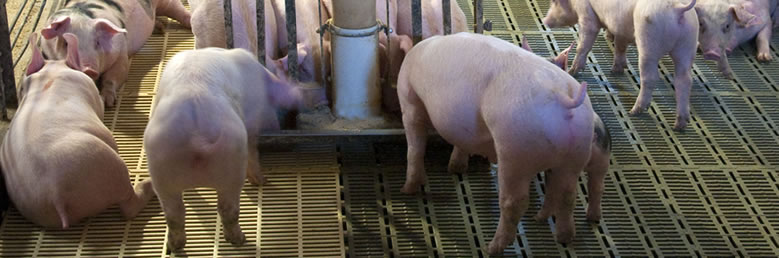
Hatchery:
Agroporc has a high-tech pig farm, with a full-cycle confinement system, which means that all production is carried out indoors, in specially adapted sheds, to optimize pig growth. The production system is characterized by using improved genetic lines, which are adapted to the new consumption standards, delivering homogeneous quality products with low cholesterol levels and a large percentage of lean meat.
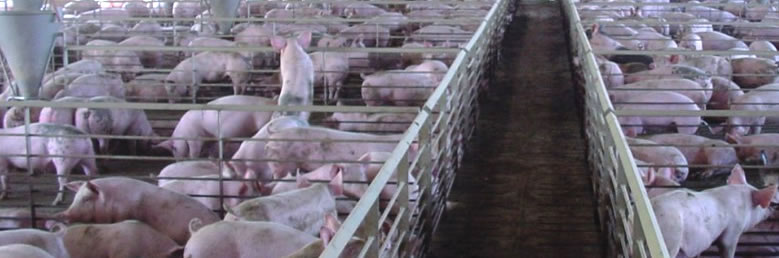
Growth and Completion:
To optimize the growth of the pigs, the gestation time is 114 days, which is known as the 3 months, 3 weeks and 3 days necessary for the sows to give birth.
At birth, the young are housed with their mothers for 21 days, where they reach approximately 6 kilos and are weaned.
They enter the rearing stage, up to 70 days, when they acquire an approximate weight of 28 kilos. At that time, the stage known as growth and completion begins, which lasts up to 165 days. When the animal reaches the required final weight, which ranges between 108 and 111 kilos, it is transferred to the refrigerator facilities, where the slaughter is carried out.
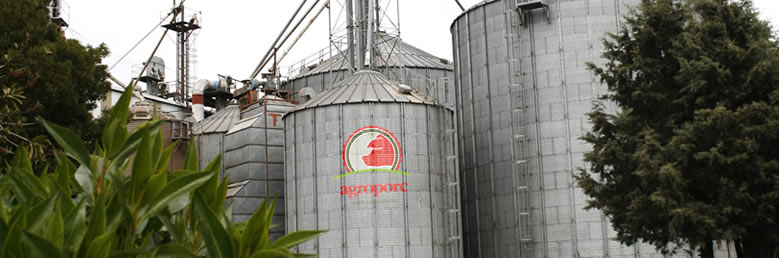
Feeding:
The effort of the sector is very important, in order to achieve efficiency in the use of the nutrients ingested by the pig. The diet is basically made up of a rigorous diet of corn, milk, soy, vitamins and minerals that meet the nutritional objectives and intensify the final quality with which the animals come out.
From health, it also contributes to the common objective of the area: the highest quality of the final product, which is why the company draws up and controls its biosafety, health and immunity programs, such as those for monitoring residues, pathogenic microorganisms and microbiological.
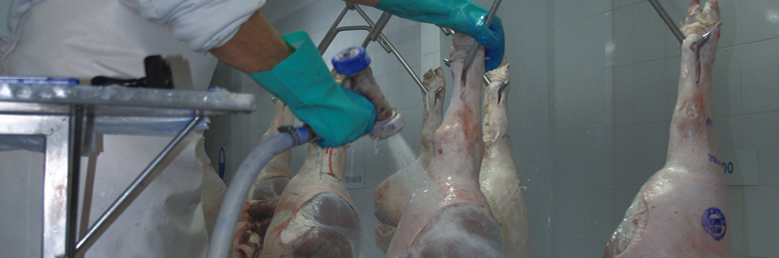
Processing plant:
Two completely independent lines of work are developed at the plant: slaughter and stripping. The processing plant has the incorporation of modern cold stores, providing the plant with an important refrigeration and freezing capacity, which allows an integral management of the cold chain, in the entire production circuit. In order to guarantee the quality of the final product, the rest and maturation of the half-reeds is respected.